PARTS AND EQUIPMENT
HOT MELT SYSTEMS
WALMARK SUPPLIES PARTS TO FIT YOUR
VALCO MELTON AND NORDSON EQUIPMENT.
Walmark is a direct partner of Valco Melton and is proud to offer
their industry leading adhesive equipment and parts.
HOT MELT HOSES
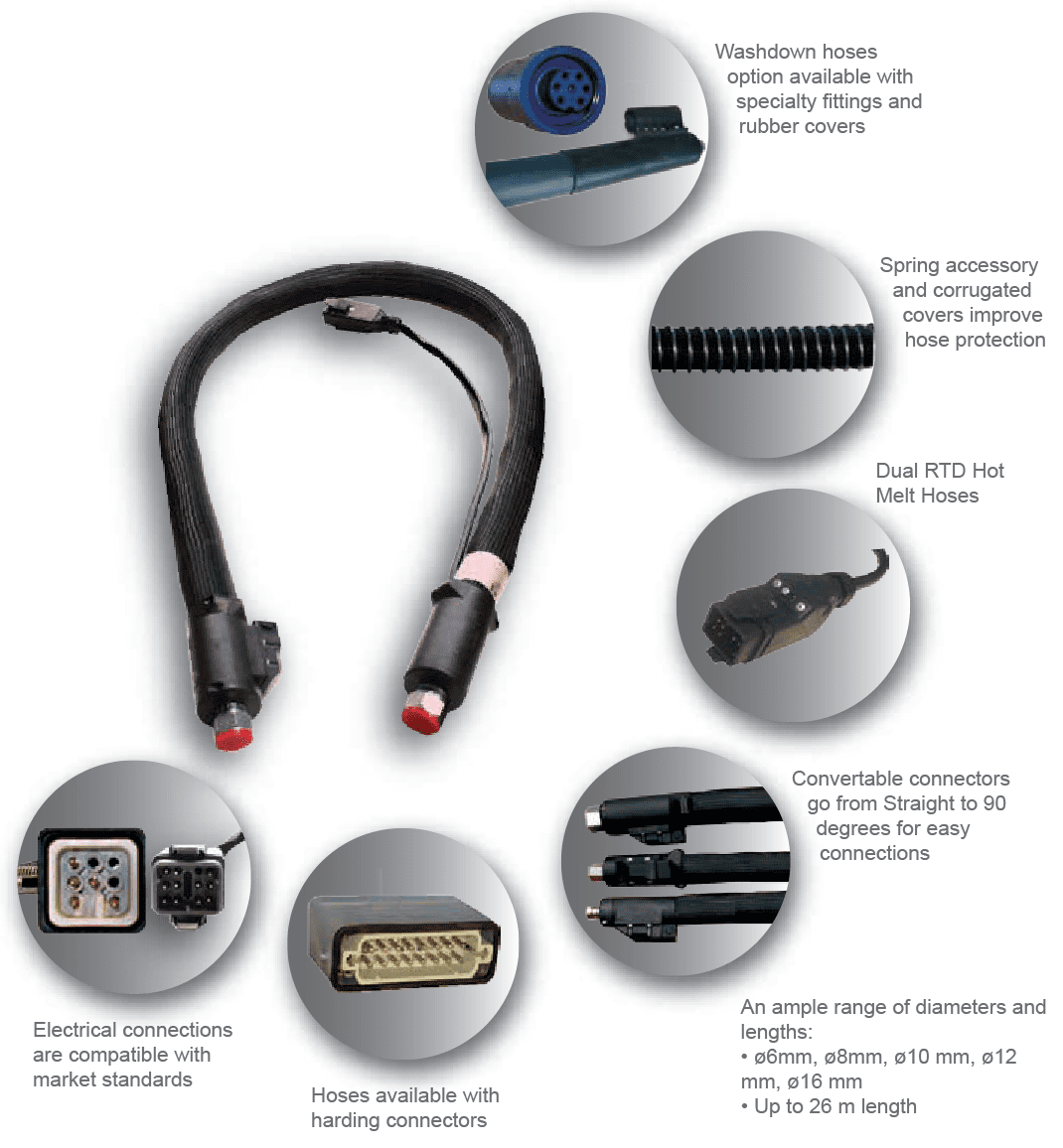
Engineered for Durability and Longevity
As a world leader in adhesive application engineering, Valco Melton is able to offer a larger range of hot melt hoses with improved market standard adaptability. Valco Melton hoses are the ideal solution for quality hot melt transport and optimal benefits.
- Industry standard compatible
- Flexible
- Interchangeable
- Versatile & dependable for all applications
- Proven design & quality guaranteed
- Long lasting design to remain "char" free
- "Nomex" and Flex Foam insulation for the best insulation and temperature stability in the industry
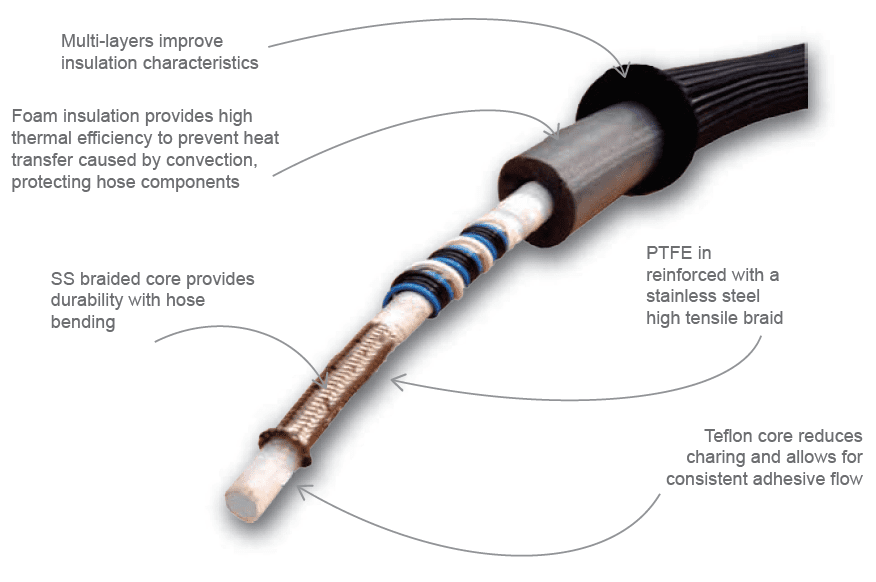
- Valco Melton manufactures hot melt hoses using top of the line market components that are 100% mechanically and electronically interchangeable
- Hot Melt Hoses are temperature sensored by Ni-120 or PT-100 RTD
- Accessories include brackets, fittings, hose protectors, corrugated and braided covers
- Valco Melton hoses are CE certified
TECHNICAL SPECIFICATIONS
MAXIMUM WORKING TEMPERATURE | 220°C | 220°C | 220°C | 220°C |
INTERNAL DIAMETER (mm) | ø8 | ø13 | ø16 | ø20 |
MAXIMUM WORKING PRESSURE (bar) | 100 | 100 | 100 | 80 |
POWER CONSUMPTION (W/m) | 150 | 175 | 195 | 200 |
RTD | PT-100/ NI-120/ NTC 1000/ FEKO | PT-100/ NI-120/ NTC 1000/ FEKO | PT-100/ NI-120/ NTC 1000/ FEKO | PT-100/ NI-120/ NTC 1000/ FEKO |
MINIMUM CURVATURE RADIUS (180°) | 160 mm | 160 mm | 160 mm | 160 mm |
VOLTAGE | 200 - 240 VAC | 200 - 240 VAC | 200 - 240 VAC | 200 - 240 VAC |
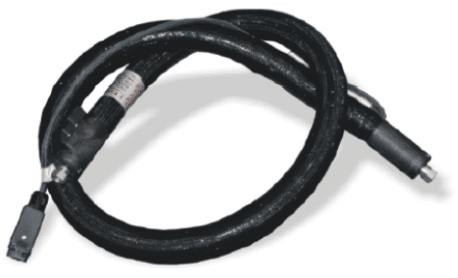
HOSE CORE SIZE | TUBE SIZE | JIC THREAD |
#4 | 1/4 in | 7/16-20 |
#6 | 3/8 in | 9/16-18 |
#8 | 1/2 in | 3/4-16 |
#10 | 5/8 in | 7/8-14 |
#12 | 3/4 in | 1 1/16-12 |
The standard hoses used with all Valco Melton equipment are compatible with Nordson 2300/3000 Series, Problue and Durablue. All Valco Melton hoses are built using the best materials available. Each hose is wound with Nomex insulation providing the best insulation and energy efficient performance. All standard hoses use a 3/8" ID core with high flex capability.
There are several types of hoses available. The washdown hoses use a different connection on the applicator end of the hose. These hoses must be used with washdown applicators. The Swirl/Spray hoses are similar to the standard hose but house an internally wound air line that heats the air used in swirl applications. The tubing protrudes through both ends of the hose. Typically, the tubbing on the unit end is connected to an air regulator and the tubing on the applicator end is connected to either a swirl handgun or automatic applicator.
HOT MELT MODULAR GUNS
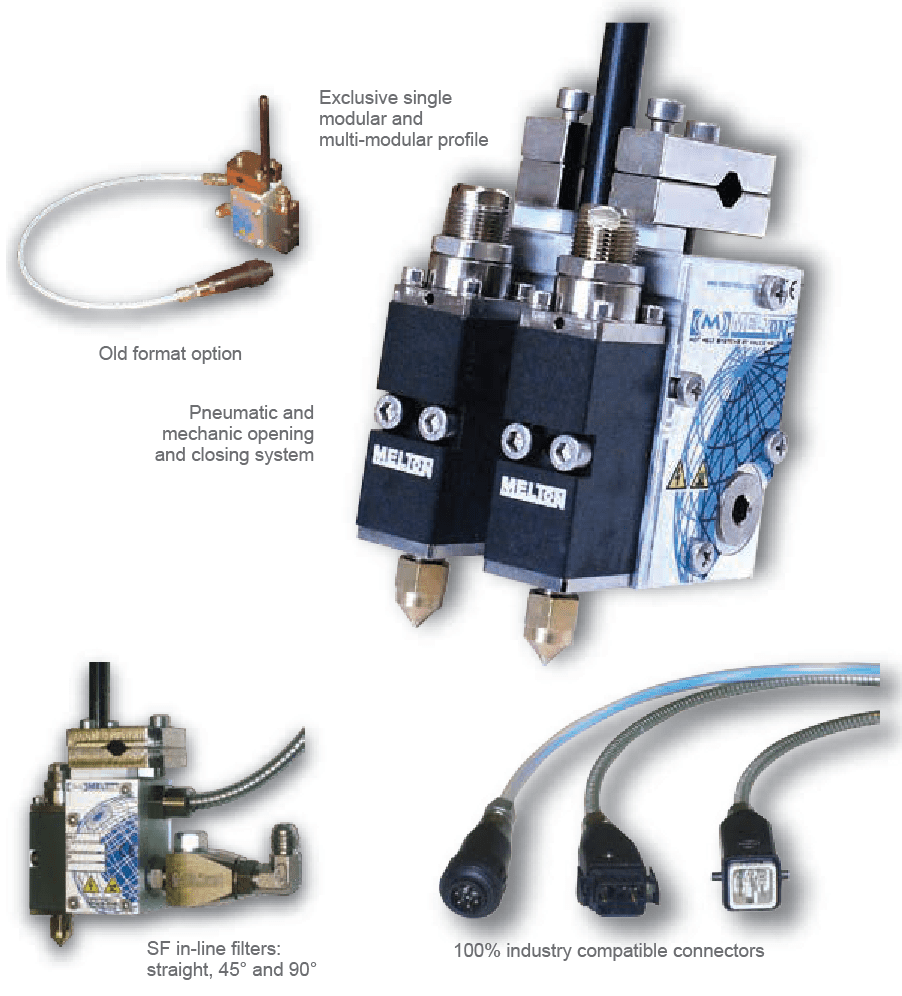
MS SERIES
The new Valco Melton MS Series offers precise and flexible control for a variety of dispensing applications, ensuring optimal uniformity and quality. The MS Series features and industry standard compatible platform, easy-to-access heaters and RTD's, as well as multiple fluid port locations. All MS gun manifolds utilize high quality components and universal mounting brackets for easy configuration into any installation. The MS Series is available in both standard and washdown cordset options and are adaptable to any in-line filter assembly. The MS Series also uses an exclusive and unique single and multi-modular design for greater flexibility and faster delivery times.
GET THESE IMMEDIATE BENEFITS
- 100% Compatibility with other industry standard spare parts
- Improve production levels with high performance
- Flexible to your work requirements
- Durable design
- Manufactured and quality tested for reliability and accurate adhesives placement
- Choose from the largest variety of compatible modules and nozzles in the industry to fit your exact needs
- CE Certified
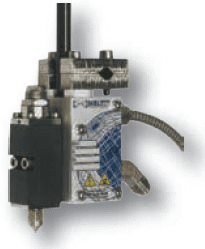
MS STANDARD BEAD
These are the standard nozzles used on all MS, ME and LP style guns. They are also fit for Nordson Classic Blue, H-200, Solid Blue and ME modules. the Valco Melton nozzles are machined from a brass body and have a stainless insert. The inserts are formed from medical grade polished capillary tube which provides the highest quality channel from which the adhesive can be extruded. These nozzles will provide a straight, consistent, and accurate adhesive bead.
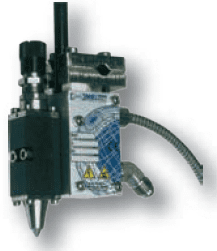
MS CVO and CVR
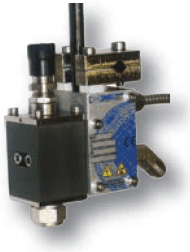
MS CHO and High Flow
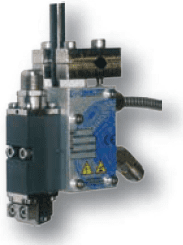
MS L20 and Multi-Line
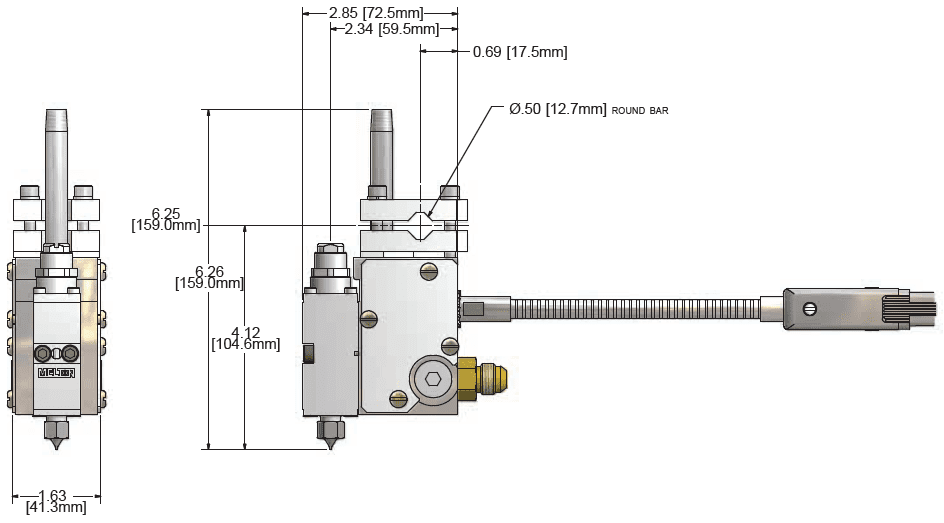
MS SERIES TECHNICAL SPECIFICATIONS
MAXIMUM HYDRAULIC PRESSURE | 100 bar |
MAXIMUM TEMPERATURE | 240°C |
TEMPERATURE SENSOR | Ni120, PT 100, FEKO, NTC |
PNEUMATIC PRESSURE | 4 - 6 bar |
OPENING SYSTEM | AOSC |
MAX CYCLE RATE | 2400 cycles/min |
SINGLE ORIFICE H200 NOZZLES
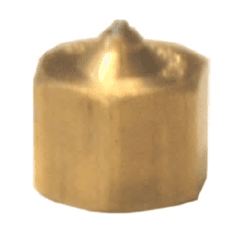
NOZZLES
These are the standard nozzles used on all MS, ME and LP style guns. They are also fit for Nordson Classic Blue, H-200, Solid Blue, and ME modules. the Valco Melton nozzles are machined from a brass body and have a stainless insert. The inserts are formed from medical grade polished capillary tube which provides the highest quality channel from which the adhesive can be extruded. These nozzles will provide a straight, consistent, an accurate adhesive bead.
GEAR PUMP HOT MELT UNITS
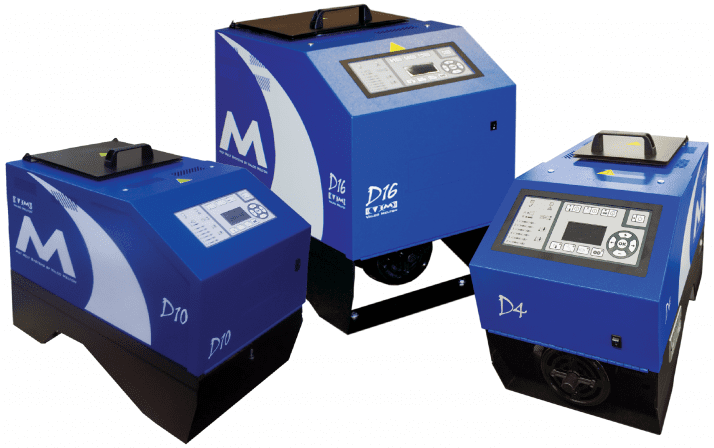
For ease-of-use, a unified operator interface is used across the entire range.
D SERIES - D4, D10, & D16 MELTERS
Valco Melton’s D4, D10 and D16 Series Units are ideal for packaging, graphic/print finishing, product assembly, labeling and various paper converting applications. All D Series units feature an LED display, spur gear pump with fixed or variable speed, “key-to-line” control, and a multi-functional control system. Other options include an integrated glue pattern control, line speed pressure control and integrated auto-feed systems.
GET THESE IMMEDIATE BENEFITS
- Efficient and clean operation featuring Teflon® coated tank with demand melt heating grid
- Achieve uniform output pressure to match line speed with built-in pressure run-up control.
- Reduce dynamic seals and wear-components with the all-electric gear pump and motor.
- Easy-to-connect HMI communication through the melter interface I/O's.
- Avoid compatibility problems with Valco Melton's industry standard hoses, guns, and tank filters.
- Complies with major approval codes worldwide.
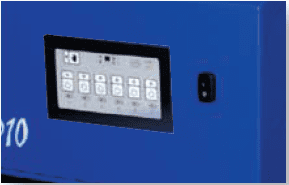
D10 and D16 Units feature an optional integrated pattern control, capable of 6 outputs and 4 inputs along with line speed tracking. PID Controls provide precise RTD temperature sensing that optimize power usage and system performance.
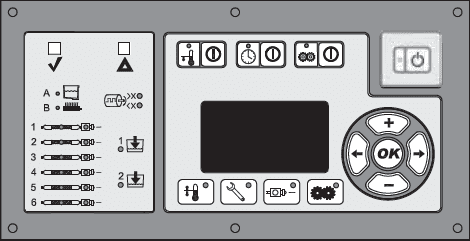
Eliminate complicated programming tasks with the user-friendly, multi-functional PID controller, which allows operators to quickly configure system parameters and monitor operation.
D4, D10, & D16 SERIES MULTI-FUNCTIONAL PID CONTROLLER FEATURES:
- Multi-language display
- Programmable sequential zone start-up
- Automatic temperature setback
- High/low temperature protection
- Fahrenheit or Celsius option
- System diagnostics
- Ethernet IP temperature control interface
- Seven-day programmable clock
- Digital RPM readout
- Optional Low-level detection in tank
- Optional variable-speed motor control
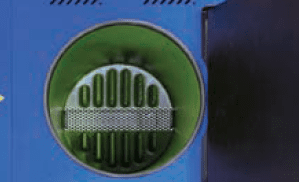
Maximize melt rate and efficiency using the Teflon® coated tank with custom fin design.
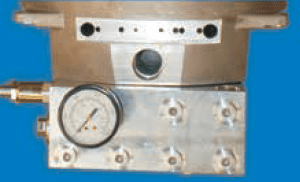
D10 and D16 units feature easier cleaning and maintenance with a 6 output manifold and integrated tank shutoff.
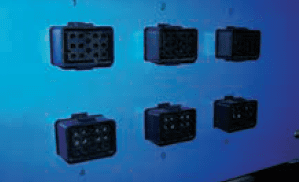
D10 and D16 units offer connections for 2,4, or 6 hoses and guns for optimal flexibility. D4 units offer connections for up to 4 hose and guns.
TECHNICAL SPECIFICATIONS
D4 | D10 | D16 | |
Gun Attachments | 2 or 4 | 2, 4, or 6 | 2, 4, or 6 |
Tank Capacity | 8.82 lb (4 kg) | 24 lb (11 kg) | 35 lb (16 kg) |
Melt Rate* | 11.1 lbs/hr (5 kg/hr) | 51 lbs/hr (23 kg/hr) | 78 lbs/hr (35 kg/h |
Pump | Motor-driven spur gear pump/ Fixed or Variable Speed | Motor-driven spur gear pump/ Fixed or Variable Speed | Motor-driven spur gear pump/ Fixed or Variable Speed |
Pump Rate | 60 lb (27 kg)/hr | 60 lb (27 kg)/hr | 120 lb (54 kg)/hr |
Temp Range | 86° - 446°F (30° - 203°C) | 86° - 446°F (30° - 203°C | 86° - 446°F (30° - 203°C |
Temp Stability | 1°F (0.5°C) | 1°F (0.5°C) | 1°F (0.5°C) |
Electrical | 208-240 VAC 1Φ/3Φ, 380 VAC 3Φ, 40 amps | 208-240 VAC 1Φ/3Φ, 380 VAC 3Φ, 40 amps | 208-240 VAC 1Φ/3Φ, 380 VAC 3Φ, 40 amps |
Weight | 75 lb (34 kg) | 109 lb (50 kg) | 120 lb (54 kg) |
Depth | 23.9 in (607 mm) | 25 in (635 mm) | 25 in (635 mm) |
Width | 12.3 in (312 mm) | 14.25 in (362 mm) | 14.25 in (362 mm) |
Height | 16.7 in (424 mm) | 21 in (533 mm) | 25.1 in (636 mm) |
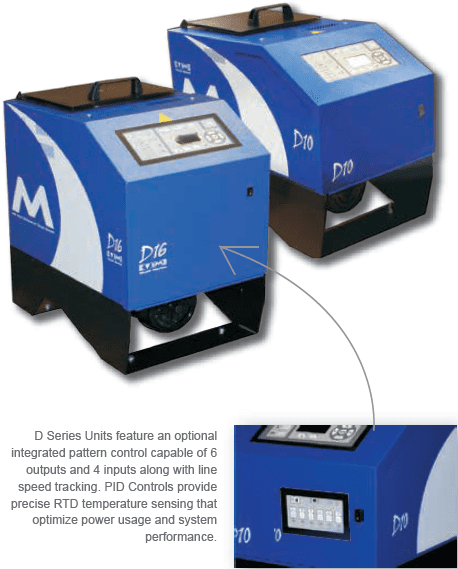
D SERIES - D10 & D16 MELTERS
For ease-of-use, a unified operator interface is used across the entire range of D10 and D16 units.
GET THESE IMMEDIATE BENEFITS
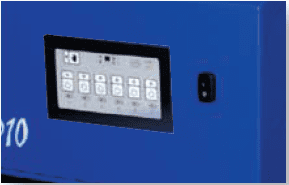
D10 and D16 Units feature an optional integrated pattern control, capable of 6 outputs and 4 inputs along with line speed tracking. PID Controls provide precise RTD temperature sensing that optimize power usage and system performance.
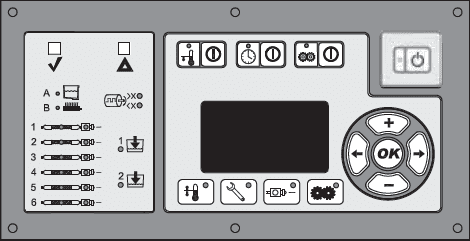
D10 and D16 Units feature an easy-to-use touchpad with a bright LCD display screen to allow operators to quickly setup system parameters and monitor system operation.
D4, D10, & D16 SERIES MULTI-FUNCTIONAL PID CONTROLLER FEATURES:
- Multi-language display
- Programmable sequential zone start-up
- Automatic temperature setback
- High/low temperature protection
- Fahrenheit or Celsius option
- System diagnostics
- Ethernet IP temperature control interface
- Seven-day programmable clock
- Digital RPM readout
- Optional Low-level detection in tank
- Optional variable-speed motor control
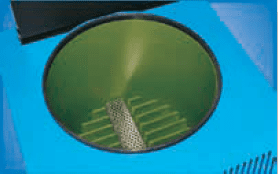
Teflon® coated tanks with custom fin design maximize melt rate and efficiency.
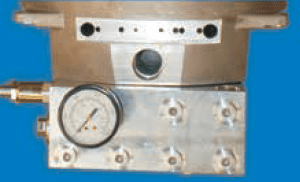
6 Output manifold with integrated tank shutoff for ease of cleaning and maintenance.
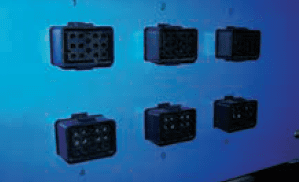
Outlets for six hoses and guns allows for optimal flexibility.
TECHNICAL SPECIFICATIONS
D10 | D16 | |
Gun Attachments | 2, 4, or 6 | 2, 4, or 6 |
Tank Capacity | 24 lb (11 kg) | 35 lb (16 kg) |
Melt Rate* | 51 lbs/hr (23 kg/hr) | 78 lbs/hr (35 kg/h |
Pump | Motor-driven spur gear pump/ Fixed or Variable Speed | Motor-driven spur gear pump/ Fixed or Variable Speed |
Pump Rate | 60 lb (27 kg)/hr | 120 lb (54 kg)/hr |
Temp Range | 86° - 446°F (30° - 203°C | 86° - 446°F (30° - 203°C |
Temp Stability | 1°F (0.5°C) | 1°F (0.5°C) |
Electrical | 208-240 VAC 1Φ/3Φ, 380 VAC 3Φ, 40 amps | 208-240 VAC 1Φ/3Φ, 380 VAC 3Φ, 40 amps |
Weight | 109 lb (50 kg) | 120 lb (54 kg) |
Depth | 25 in (635 mm) | 25 in (635 mm) |
Width | 14.25 in (362 mm) | 14.25 in (362 mm) |
Height | 21 in (533 mm) | 25.1 in (636 mm) |
ADHESIVE MELTER WITH MULTI-FUNCTIONAL CONTROL
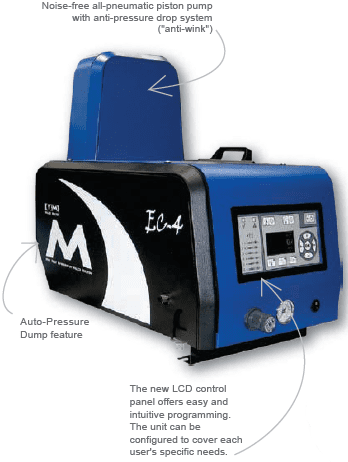
For ease-of-use, a unified operator interface is used across the entire range.
EC SERIES - EC4, EC8, EC14, EC30, & EC50
- High Performance, multi-functional option-filled hot melt application solutions
- LCD Operator Panel for ease of use and programming
- Optional Integrated Auto Feed System and Glue Pattern Control
- Common footprint allows for universal installation
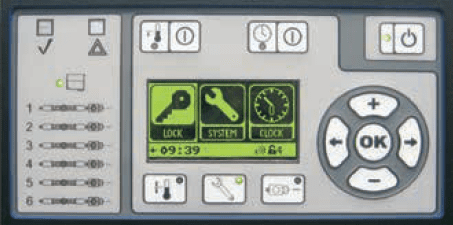
EC UNIT MULTI-FUNCTIONAL CONTROLS
- Separate LED indicator for each zone
- An alarm system with outputs
- Direct access button to setback/standby mode
- Configuration screen with intuitive interface and LED indicator for configuration mode
- Up to 3 different daily programs for each day of the week
- New MCP6-P fully integrated adhesive pattern control included in option
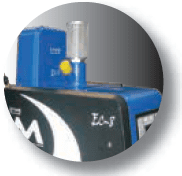
Optional, fully-integrated autofeed system increases safety and prevents overfilling.
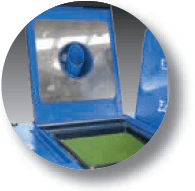
The lid includes a reservoir seal that reduces contamination and insulates molten adhesive.
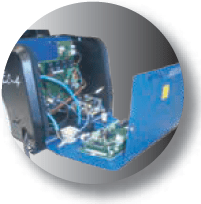
NEW lid feature for easy access to electronic components.
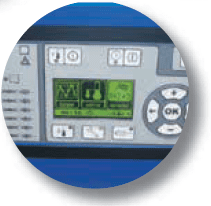
7 day / 3 shift programmable clock.
Reduces setup and increases efficiency.
TECHNICAL SPECIFICATIONS
Unit | EC 4 | EC 8 | EC 14 | EC 30 | EC 50 |
Tank Capacity (lt) | 4 lt | 8 lt | 14 lt | 30 lt | 50 lt |
Melt Rate (Kg/h) | 6 | 9 | 13, 5 | 20 | 35 |
Pump Compression Rate (Kg/h) | 1:14 | 1:14 / 1:13 | 1:13 | 1:13 | 1:13 |
Max. Pump Capacity (Kg/h) | 35 | 35 / 100 | 100 | 100 | 100 |
Working Temp Range | 30 - 240°C | 30 - 240°C | 30 - 240°C | 30 - 240°C | 30 - 240°C |
Electrical Connections | 220 I + T, 220III + T, 380III +N+T | 220 I + T, 220III + T, 380III +N+T | 220 I + T, 220III + T, 380III +N+T | 220 I + T, 220III + T, 380III +N+T | 220 I + T, 220III + T, 380III +N+T |
Working Viscosity (cps) | 50,000 cps | 50,000 cps | 50,000 cps | 50,000 cps | 50,000 cps |
Pneumatic Pressure (bar) | 0.5 - 6 bar | 0.5 - 6 bar | 0.5 - 6 bar | 0.5 - 6 bar | 0.5 - 6 bar |
Electrical Consumption (W) | 1800 w | 2800 w | 4000 w | 4000 w | 4000 w |
Max Channel Power (W) | 1 -2 Exits | 3, 4, 5, 6, 7, 8 Exits |
Total Hose + Gun | 1800 w | 1450 w |
Per Exit (Hose & Gun) | 1800 w | 1450 w |
Per Channel (Hose & Gun) | 1800 w | 1450 w |
Dimension (mm) | EC 4 | EC 8 | EC 14 | EC 30 | EC 50 |
A | 532 | 532 | 592 | 782 | 822 |
B | 307 | 307 | 367 | 558 | 598 |
C | 340 | 340 | 340 | 376 | 526 |
D | 583 | 658 | 658 | 943 | 943 |
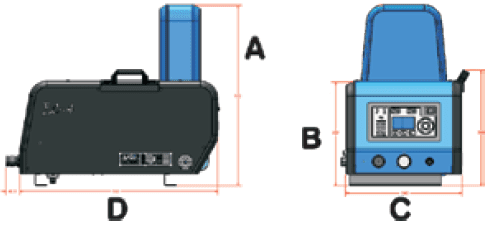
ECOSTITCH™ GLUING SOLUTIONS
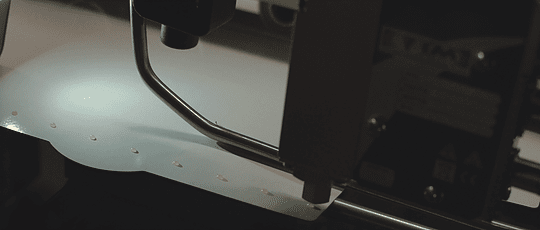
- Reduce adhesive usage up to 80%
- Can adapt and be fitted to your existing gluing systems
- Eliminate compressed air from system operation
- Minimize parts changes & downtime
- Lower pressure + larger orifice = no nozzle plugging
- Up to 2 billion activation cycles before service is required
- Minimize angel hair or stringing
EASY INTEGRATION OPTIONS
EcoStitch can be added to your existing machine or as a full system.
FULL SYSTEM
CONVERSION
Includes a gear pump melt unit, pattern control with EcoStitch™ technology, and MX electric valves.
OEM SYSTEM
CONVERSION
Includes a gear pump melt unit, valve drivers with EcoStitch™ control (that utilizes existing PLC recipe) and MX electric valves.
BETTER BONDS, LESS ADHESIVE & WHY THIS WORKS!
The bonding surface area of the dots provide more adhesion and coverage per square mm of adhesive placed.
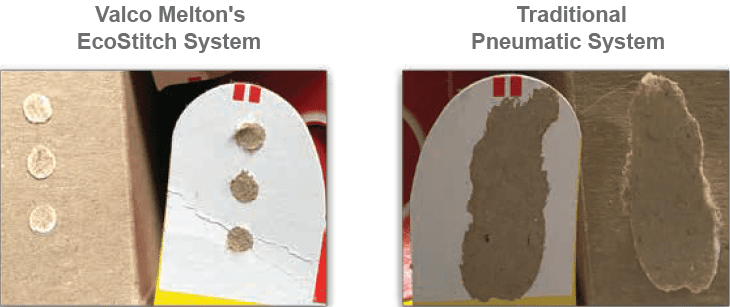
MORE ECOSTITCH CASE & CARTON SEALING APPLICATIONS
Whether on carton stock or corrugated, the EcoStitch bond provides a cleaner, stronger and more flexible bond than traditional beads.
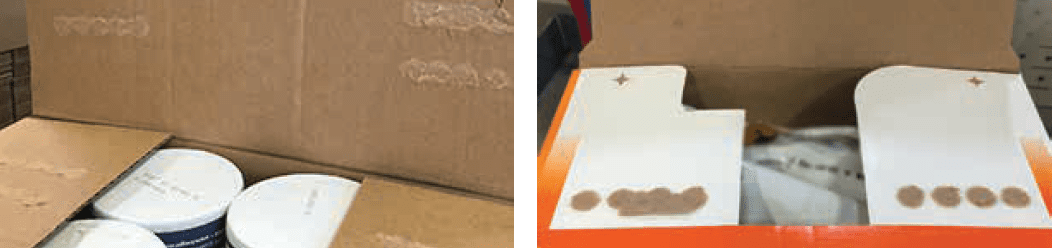
WHY ECOSTITCH ALL-ELECTRIC SYSTEMS LAST LONGER THAN PNEUMATIC
By eliminating dynamic seals and compressed air from system operation, you minimize your chance of valve failure, the cost to replace spare parts and the downtime associated with it.
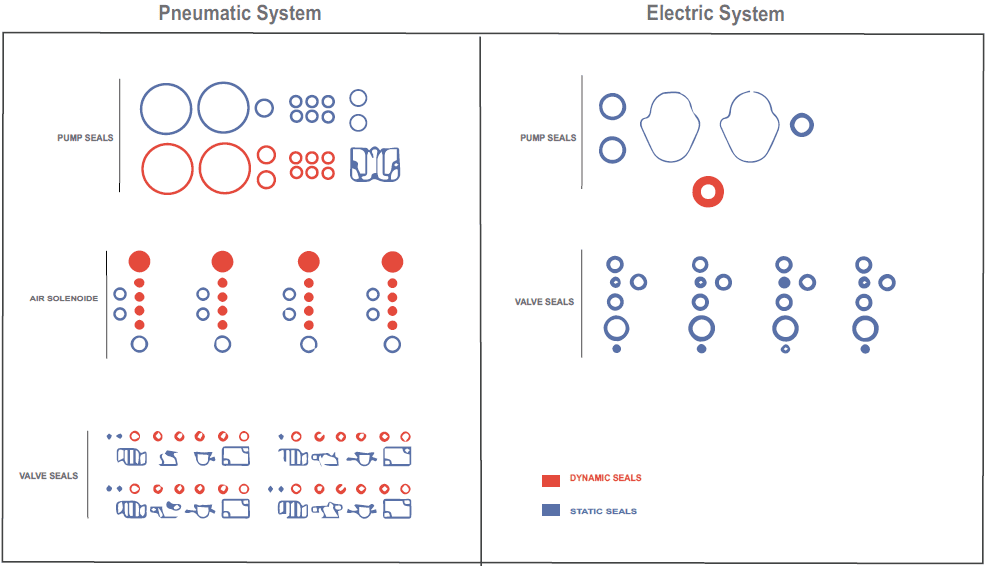
ELECTRIC VS PNEUMATIC SYSTEMS
• Eliminates plant air
• Fewer parts
• Fewer dynamic seals
• Longer parts life
• Cleaner running
• More consistent pump pressure
![]() | ![]() This graphic demonstrates how the dynamic (Red) seals show potential for wear and replacement. Valco Electric systems almost eliminate these points of failure, saving you money and keeping your production running! |
ALL-ELECTRIC ADHESIVE DISPENSING VALVE FEATURING ECOSTITCH TECHNOLOGY
Valco Melton's MX electric hot melt valve is the workhorse for most Valco Melton hot melt dispensing solutions. The MX electric valve can operate at extremely high speeds reaching 15,000 cycles per minute for short bursts and have a lifetime capable or more than 2 billion cycles depending on operating conditions. The MX electric valve is used for many different applications including Packaging, Folding Carton, Sift Proof Packaging and Slot Coat applications. The MX is widely known as the EcoStitch capable valve in Food and Beverage packaging where end users see their adhesive usage reduced by up to 75% for instant ROI and process improvement.
ECOSTITCH DRIVERS AND PATTERN CONTROLS
Valco Melton's Pattern Controls provide a customized signal that fires the EcoStitch MX Valve.
VD Drivers provide EcoStitch control utilizing existing PLC recipes.
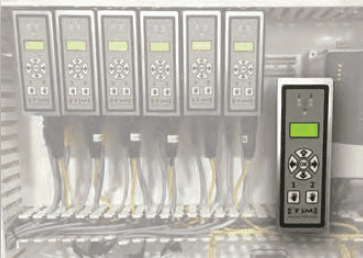
VD2 Panel Mount
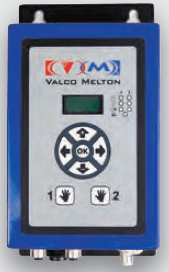
TECHNICAL SPECIFICATIONS
EcoStitch™ Characteristics
Valve Width | 22 mm (0.860 in) |
Valve Height | 155 mm (6.10 in) |
Mounting | 12.70 mm (0.500 in) round bar |
Fluid Pressure | 70 bar (1000 psi) |
Life Cycle | 2 billion cycles* |
Max Cycle Rate | 15,000 cycle/min for short durations |
Performance | 2 msec dispense, 2 msec gap |
* Depending on operating conditions
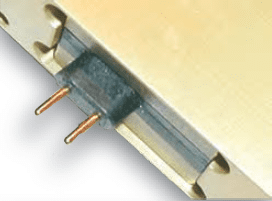
The "quick-connect" coil allows for easy change-outs between valve configurations. All the connections to melt units are 100% compatible with existing hot melt equipment.
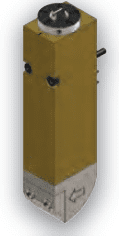
The MX Slot Coat module is ideal for narrow web coating and intermittent slot coat application. This MX valve can work with any of the standard and Multi-Module Applicators.
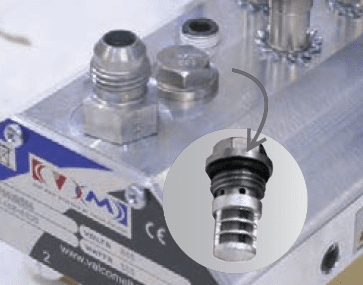
The EcoStitch™ Applicator comes standard with an integrated filter in the manifold.
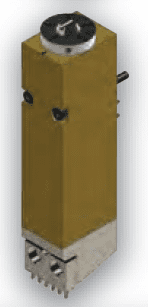
The MX Sift Proof module is ideal for sift proof applications in food packaging applications with granular material as well as in book binding for hard back spine gluing. The blade sets can be configured for up to 6 mini lines per module and is compatible with both the Standard and Multi-Module Applicators.
KUBE SYSTEM
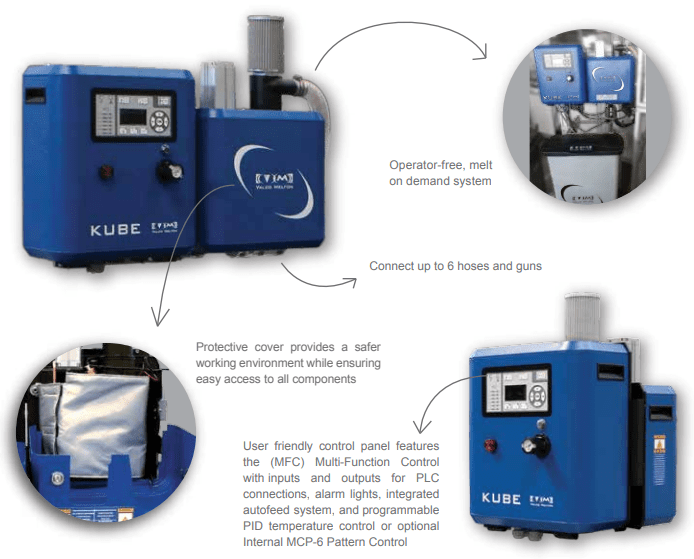
BETTER BONDS, LESS ADHESIVE & WHY THIS WORKS!
- Promotes adhesive stability and reduces char by only melting adhesive as needed
- No more plugged nozzles. Automatic feeding keeps contaminants out
- Multiple mount configurations make the Kube suitable for new machine installations or to retrofit existing equipment
- Fully compatible with other industry standard hoses, guns, or spare parts
- Auto Pressure Dump feature eliminates pressure when machine is open for safer operation
BETTER BONDS, LESS ADHESIVE & WHY THIS WORKS!
MELTING CAPACITY | Up to 9 kg/h |
MAX HYDRAULIC PRESSURE | 80 Bar |
PUMPING CAPACITY | 35 kg/h |
MAX VISCOSITY | 30.000 cps |
ELECTRICAL POWER | 2460 W |
ELECTRICAL CONNECTIONS | 230 I + N + T, 230 III +T, 400 III +N + T |
TEMPERATURE RANGE | 15° - 230°C |
ESTIMATED AIR CONSUMPTION | 50 - 90 L/min. |
MAX CHANNEL POWER (W) | 1 - 2 EXITS | 3, 4, 5, 6 EXITS |
PER EXIT (HOSE & GUN) | 1800 W | 1450 W |
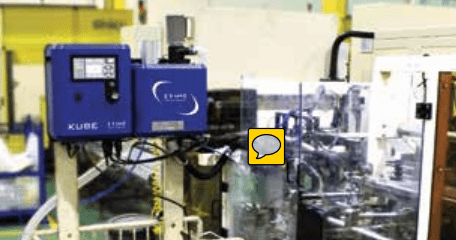
Engineered to operate with three different mount configurations, the Kube is suitable for both new machine installations, as well as system upgrades/ replacements.
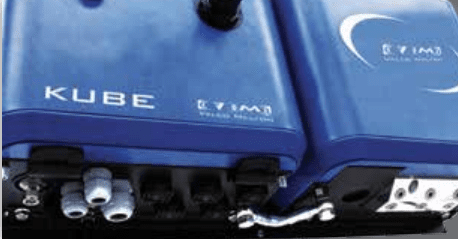
Fully compatible with other market standards, the Kube can run up to 6 hoses/ guns with no ties to any brand or model.
Dimensions (mm) | ![]() PANEL | ![]() | ![]() |
HEIGHT (mm) | 450 | 580 | 450 |
LENGTH (mm) | 770 | 280 | 308 +480 |
DEPTH (mm) | 250 | 550 | 250 |
SERVICE IS OUR PRIMARY PRODUCT.